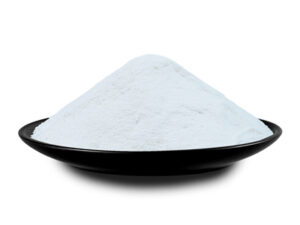
What Is Sodium Tripolyphosphate Used For
Sodium tripolyphosphate (STPP) is a versatile chemical compound that is crucial in detergents, water treatment, food processing, ceramics, and many industrial applications.
As a sodium tripolyphosphate (STPP) manufacturer, understanding the differences in the characteristics of type I and type II crystals is crucial for detergent formula design.
The difference between sodium tripolyphosphate type I (high-temperature type) and type II (low-temperature type) stems from the coordination mode of sodium ions in the crystal structure:
Dissolution rate and thermal stability
Type I: fast dissolution rate (suitable for liquid detergents that need to be dispersed quickly) but low thermal stability (easily transformed to type II above 417°C).
Type II: slow dissolution rate but high thermal stability (stable below 400°C), suitable for high-temperature production process.
Hygroscopicity and agglomeration risk
Type I: strong hygroscopicity, significant hydration heat release, easy to cause powder agglomeration (such as common problems in laundry detergent storage).
Type II: slow moisture absorption, better powder fluidity, suitable for high humidity environment
Density difference
Type I has a 2.62 g/cm³ density, while Type II has a 2.57 g/cm³ density, affecting detergents’ bulk density design.
1. Liquid detergents
Type I is recommended. Its fast dissolution characteristics can improve the formula’s uniformity and avoid liquid stratification (such as concentrated laundry detergent). To enhance the chelating ability, it needs to be matched with the synergistic effect of additives (such as sodium pyrophosphate).
2. Powdered detergents
Type II is preferred: Low hygroscopicity can reduce the problem of caking in storage, and anti-caking solutions (such as adding silica) can extend the shelf life.
3. Low-temperature formulas and environmentally friendly products
Type II is recommended: It complies with the trend of environmental regulations and compliance (such as the EU phosphorus restriction policy) and is suitable for low-temperature washing scenarios (such as cold water laundry detergent).
Problem background: A manufacturer uses Type I STPP to produce laundry detergent, which suffers from severe caking in Southeast Asia’s high temperatures and high humidity, resulting in customer complaints.
Solution:
Crystal form replacement: switch to type II STPP to reduce moisture absorption by 30%.
Process optimization: adjust spray drying parameters to control the moisture content of powder to ≤0.1%.
Warehouse upgrade: use moisture-proof packaging and temperature-controlled warehousing to control humidity below 50%.
Result: The agglomeration rate decreased by 85%, and the customer repurchase rate increased by 20%.
1. Crystal form selection by mainstream manufacturers
According to 2025 production capacity data (Huajing Industry Research Institute):
Industrial-grade STPP: Type II accounts for more than 60% (due to shrinking demand for detergents, turning to industrial cleaning agent ingredients, and flame retardant material development).
Food-grade STPP: Type I dominates (must comply with food additive standards, such as GB2760-2011).
2. Export market analysis
The export volume of food-grade STPP increased from 16% in 2015 to 38% in 2022, mainly to emerging markets such as Brazil and Thailand.
Industrial exports are concentrated in Indonesia and India, and attention should be paid to the trend forecast of the phosphorus chemical industry (such as the impact of phosphorus-free substitutes).
Production process optimization: The spray drying-converter polycondensation two-stage method improves type II purity (whiteness ≥ 90%).
Compliance layout: Adapt to environmental protection regulations in advance (such as China’s “phosphorus restriction” policy) and develop alternatives such as layered sodium silicate.
High added value expansion: Explore the application of food-grade STPP in improving the water retention of meat products and the quality of noodle products.
Sodium tripolyphosphate (STPP) is a versatile chemical compound that is crucial in detergents, water treatment, food processing, ceramics, and many industrial applications.
Sodium Tripolyphosphate (STPP): A detailed analysis of its chemical properties, industrial uses, and essential safety guidelines for handling and application.
Sodium tripolyphosphate improves food texture, yield, and shelf life, making it a vital additive in industrial food processing.
Sodium tripolyphosphate (STPP) enhances detergents through water softening, soil suspension, and pH buffering via its unique phosphate chemistry.
Sodium Tripolyphosphate (STPP) is a widely used sodium-based compound critical in various industries, from detergents and water treatment to food processing and pharmaceuticals.
Sodium tripolyphosphate (STPP) enhances detergents through water softening, soil suspension, and pH buffering via its unique phosphate chemistry.
Sodium tripolyphosphate (STPP) is manufactured through controlled reactions of phosphoric acid and sodium compounds, with patented industrial processes optimizing purity and yield.
Sodium tripolyphosphate (STPP) effectively softens water in detergents while serving as a preservative in food applications, demonstrating remarkable versatility.
The leading factory for sodium tripolyphosphate in China with fast delivery, free sample and fantastic services.
@ 2024 Sodium Tripolyphosphate. All right reserved.
WhatsApp us