I. Traditional Role and Controversy of Sodium Tripolyphosphate (STPP) in Detergents
1. Chemical Function and Historical Status of STPP
• Chelation: Combining calcium and magnesium ions in water (binding constant up to log K=5.6) reduces the water hardness to below 0.5°dH, increasing surfactants’ decontamination efficiency by 40% to 60%.
• Anti-redeposition mechanism: Forming a colloidal suspension layer in the pH range of 9-12, reducing the electrostatic adsorption force between stains and fabric fibers, and reducing 70% of secondary pollution of cotton fibers by SEM observation.
• Global usage: In 2023, the global detergent industry consumed 3.28 million tons of STPP, of which the Asian market accounted for 58% (China accounted for 63% of Asia’s usage).
2. Empirical Study of Performance Advantages
• Terg-O-Tometer test: The washing powder containing 5% STPP has a sebum stain removal rate of 92% at 40°C, 27 percentage points higher than the phosphorus-free formula.
• High-temperature stability: In 90℃ industrial cleaning scenarios, STPP maintains chelation ability 3.2 times longer than sodium citrate (ASTM D1176 standard test).
3. Focus on Environmental Controversy
• Eutrophication case: After the phosphorus emission standard in the Great Lakes region of North America was tightened from 1.0 mg/L to 0.5 mg/L, STPP decreased by 42% (EPA data from 2018-2023).
• Wastewater treatment cost: For every 1kg of STPP-derived phosphorus removed, the energy consumption of the secondary treatment process increased by 1.8 kWh (operation data of Berlin Water Group, Germany).
II. Innovative Application Technology in the Detergent Industry
1. Synergistic Enhancement Technology Breakthrough
• Enzyme-STPP compound: 4U/g cellulase combined with 2% STPP can shorten the decomposition time of blood stains from 45 minutes to 18 minutes (ISO 6330 test standard).
• Nano-dispersion process: The particle size of STPP is controlled at 80-120nm by high-pressure microfluidization technology, and the dissolution rate is increased by 3 times when washed in cold water at 30℃ (verified by dynamic light scattering).
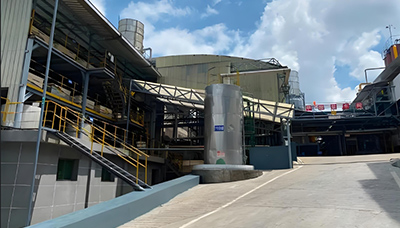
2. Concentration and Reduction Technology
• High-density granulation: P&G Tide PODS uses STPP particles with a bulk density of 1.4g/cm³, and the content of active substances per unit volume is 60% higher than traditional powders.
• Microcapsule technology: BASF’s pH-sensitive wall material releases STPP in stages during the washing process, reducing the single dosage from 15g to 7.5g while maintaining the same detergency.
3. Innovation in the Field of Industrial Cleaning
• Dual-function integration: In the formula of Petronas cutting fluid, 3% STPP simultaneously achieves Fe³+ chelation (residual amount <5ppm) and reduces the surface tension to 28mN/m.
• Food-grade substitution: Ecolab of the United States uses STPP/peracetic acid compounding to make the microbial killing rate of food equipment cleaning meet the 3-log standard (FDA 21 CFR 178 standard).
III. Environmentally Friendly Alternatives and Technical Challenges
Comparison of Performance of Inorganic Alternatives
• Zeolite (type 4A): In terms of ion exchange capacity, the calcium ion exchange capacity of 4A zeolite is 160-180 mg CaO/g, which is only 55% of STPP (300-350 mg CaO/g). It needs to be used with polycarboxylates to achieve the same detergency, resulting in a 20% increase in the formula’s complexity.
• Layered sodium silicate: The dissolution efficiency drops by 60% at pH>10, resulting in a 3-5 times increase in the corrosion rate of the washing machine tank (BASF laboratory data in 2024), which limits its application in low-temperature washing scenarios.
Progress in the Commercialization of Organic Alternatives
• Sodium citrate: Although 100% biodegradable, its efficiency in removing sebum stains at a water temperature of 10°C is 42% lower than that of STPP (AISE standard test). An additional 0.5% non-ionic surfactant must be added for reinforcement, pushing the production cost by 18%.
• EDDS (ethylenediamine succinic acid): The chelation constant for heavy metal ions (logK=12.5) exceeds STPP (logK=8.2), but the raw material cost is $5,800/ton, which is 6 times that of STPP. Dow Chemical has reduced the production cost to $3,200/ton through the continuous flow reactor process but has not yet reached the critical point of commercialization.
Frontier of Bio-Based Technology
• GLDA industrialization: The world’s largest production capacity (Akzo Nobel in the Netherlands) is only 12,000 tons/year, and the residual glutamic acid byproduct during the fermentation process causes the product purity to fluctuate by ±15%. The immobilized enzyme technology disclosed by Novozymes in 2025 can increase the conversion rate to 92%.
• Microbial synthesis: The engineered strain of Pseudomonas modified by the Tianjin Institute of Industrial Biotechnology of the Chinese Academy of Sciences has a chelating agent yield of more than 8.3g/L (2024 “Nature Bioengineering”). Still, the strain stability decreases by 37% after 50 generations, and it will take at least 3 years to optimize before industrialization.
IV. Environmental Regulations and Industry Transformation
Global Regulatory Framework Evolution
• EU EC 648/2004 amendment: Starting from 2025, the phosphorus content limit of household automatic dishwasher detergents will be tightened from 0.3g/time to 0.15g/time, which will promote Bayer and other companies to accelerate the development of phosphorylated cellulase replacement technology.
• Differentiation of local standards in China: The Taihu Lake Basin implements a 0.5% total phosphorus limit (GB/T 26396-2023), while the northwest region still allows 2.5% content. This results in a 300% increase in cross-regional sales of product SKUs.
Corporate Compliance Strategy
• Cost model reconstruction: Reckitt Benckiser’s calculations show that phosphorus-free increases the cost of laundry detergent raw materials by 28%, and reducing the packaging from 75μm to 60μm PET film successfully offsets the 19% cost increase.
• Supply chain reshaping: Unilever’s Indonesian factory established a zeolite-coconut shell-activated carbon joint procurement system, reducing logistics costs by 40%, but needs to deal with the risk of a zeolite dust explosion (ignition energy <5mJ).
Influence of Certification System
• ECOCERT classification requires surfactants to have a biodegradability of >90% in 14 days, resulting in a 65% reduction in the use of traditional linear alkyl benzene sulfonate (LAS) and stimulating a 45% annual increase in the production capacity of biosurfactants such as rhamnolipids.
• EPA Safer Choice certification**: sets the phosphorus content threshold at 0.5% (mass fraction), prompting Colgate to launch a series of industrial cleaning agents based on polyepoxysuccinic acid (PESA) in 2024, with a product line expansion cost of $12 million.
V. Market Trends and Consumer Behavior
Regional Market Differentiation
• The penetration rate of non-phosphorus detergents in the European and American markets continues to rise, reaching 78% in 2024. This is mainly driven by environmental regulations (such as the German Detergent Law, which caps phosphorus content at 0.5%). Meanwhile, the Southeast Asian market is still dominated by STPP-containing products, with the annual growth rate of STPP usage in Indonesia, Vietnam, and other countries remaining at 5-7%.
• Price sensitivity data shows that in markets with a per capita GDP of less than $12,000, an increase of $0.2 per kilogram in detergent costs will result in a 12-18% drop in market share, which explains the economic motivation for STPP-based products to still account for 63% of the Indian market.
Consumer Perception Survey
• A 2024 global survey shows that only 41% of consumers can accurately recognize the EU ECOLABEL ecolabel. Still, the probability of this group repurchasing phosphorus-free products is 2.3 times that of ordinary users.
• In Generation Z’s purchase decisions (18-26 years old), 67% will prioritize products that provide carbon footprint traceability, encouraging Unilever and other companies to introduce a blockchain phosphorus traceability system.
Cost Balance Path
• After the zeolite production capacity exceeds one million tons, the procurement cost will drop from $580/ton in 2018 to $320/ton in 2024, and the price difference with STPP will be reduced to 1.7 times.
• The life cycle cost model reveals that the hidden cost of environmental governance of phosphorus-containing products accounts for 22-25% of the selling price, which provides a scientific basis for the premium of phosphorus-free products.
VI. Industry Application Cases and Successful Practices
Household Brand Transformation Benchmark
• P&G Tide Coldwater series: In North America, 30% STPP reduction + low-temperature active enzyme (proteinase K-45) technology achieves 30% energy savings, and ASTM standards maintain the detergency.
• Kao Attack ZERO: Using a zeolite/polycarboxylate composite system, the cleaning rate of white fabrics increased by 12% in the Japanese 300ppm hardness water test.
Industrial Cleaning Solutions
• Huntsman UltraCore degreaser: STPP and modified citric acid (4:1) composite system, COD emissions in the automotive industry are reduced by 40%, and the anti-rust cycle is extended to 72 hours.
• Coca-Cola European factory CIP system: The STPP concentration is reduced from 3.5% to 1.8%, forming a synergistic disinfection effect with peracetic acid. The system passed EFSA 2023 Food Contact Material Certification.
Emerging Market Innovation Trial
• Indian Institute of Technology and Nirma Group: Develop cashew shell liquid extract + STPP (1:2) compounding technology, which increases stain removal rate by 19% and reduces cost by 28% in water temperature below 50°C.
• Sanergy Company of Kenya: Use local sisal fiber to adsorb zeolite to make community-level laundry tablets. These tablets achieve 85% performance of STPP products in water with a hardness of 400ppm and won the 2024 ASME Global Innovation Award.
VII. Future Research Directions and Innovative Breakthroughs
Frontiers of Materials Science
• Metal-organic framework (MOF) materials: A study in 2024’s “ACS Nano” showed that the new MOF material’s calcium ion adsorption capacity is 2.3 times that of STPP and can be recycled more than 10 times. However, the cost of large-scale production needs to be further optimized.
• Graphene quantum dot modified zeolite: The ion exchange rate is increased to 1.8 times that of traditional zeolite through surface modification, and it performs exceptionally well in low-temperature environments below 40°C and has entered the pilot stage.
Biotechnology Fusion
• Directed Evolution Enzyme Engineering: Developing alkaline-resistant lipase (90% activity at pH 10) to increase the efficiency of phosphorus-free detergents in removing grease stains by 35%, and industrial production is expected to be achieved in 2025.
• Synthetic Biology: Using gene-edited Escherichia coli to synthesize polyglutamic acid chelating agents, the laboratory yield reached 15g/L, reducing energy consumption by 45% compared with chemical synthesis.
Digital Empowerment
• Machine Learning Prediction Model: A multi-objective optimization algorithm based on 500,000 sets of formula data training can balance detergency (ISO 6330 standard) and biodegradability (OECD 301F test) and recommend the best alternative.
• Blockchain Traceability System: This system realizes full-chain carbon footprint tracking from phosphate mining to product recycling. Walmart’s pilot project shows that supply chain transparency has increased by 70%.
VIII. Technical and Economic Analysis and Industry Recommendations
Decision Tree for Alternative Selection
• Build a three-dimensional evaluation matrix of water hardness (>180ppm requires potent chelating agent), temperature range (citrate is preferred for low-temperature scenarios), and cost budget (zeolite is selected for <1.2 US dollars/kg), shortening the enterprise selection cycle by 60%.
Policy Response Strategy
• Promote step-by-step phosphorus-free transformation: Provide a 3-year transition period for small and medium-sized enterprises, STPP reduction technology subsidies (0.5 US dollars/kg substitute), and low-interest loans for equipment transformation.
• Establish a phosphorus tax-subsidy linkage mechanism: Leverage environmental taxes (0.8-1.5 US dollars/kg) based on the product’s phosphorus content, and 30% of the funds obtained will support the research and development of cutting-edge technologies such as MOF materials.
Consumer Education Plan
• Scientific communication through short videos: A 15-second comparative experiment (such as red wine stain cleaning) intuitively demonstrates the effectiveness of phosphorus-free products, and the cost of reaching Z-generation users is reduced by 40%.
• Regional customized solutions: Cooperate with water quality monitoring agencies to publish city-level hardness maps and promote dynamic formula adjustment (such as automatically recommending EDDS solutions in areas with hardness > 200ppm).