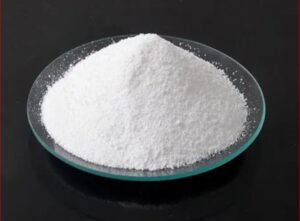
Sodium Tripolyphosphate (STPP): The Important Phosphate Additive for Modern Food and Market
Sodium Tripolyphosphate (STPP) serves as a crucial food additive that improves texture, moisture retention and shelf life in processed seafood and meat products.